Forgings are first processed by the forging factory, and the forgings are inspected after forging. Forging is to select the corresponding forging equipment according to the material, shape, size and process requirements of the forging. Forgings must be forged on the equipment specified in the process document.
Operators should be familiar with forging drawings and process documents before forging. The tools and molds used before forging must be preheated to the specified temperature by the correct method. According to the complexity of forgings, material, and process requirements, select the appropriate lubricant.
The billet should be paid attention to removing the oxide scale before and during forging. During forging, the initial forging temperature, final forging temperature, deformation degree, and deformation speed must be strictly controlled. During the forging operation, it must be carried out in strict accordance with the process regulations and process cards. Pay attention to whether the deformation of the blank is normal at any time. If any defects such as folds and cracks are found, they must be removed by appropriate methods immediately, and forging can be continued without affecting the quality of the forgings.
The cooling of forgings should be carried out according to the cooling method specified in the forging process specification. The post-forging heat treatment shall be carried out in accordance with the relevant process documents. It can be carried out according to the process regulations of the manufacturer, or according to the process requirements put forward by the user, but it must be specified when signing the contract. For Class I and II forgings, a special process specification shall be provided if necessary, and the initial production process and tooling tests shall be carried out, and they can be put into production after the verification is qualified. Class I and II forgings shall establish quality files according to the drawing numbers of the forgings.
The trimming, punching, and calibration temperature of the forgings should be carried out according to the relevant regulations of the forging process regulations. The surface of the forging should be cleaned according to the following requirements: sandblasting, shot blasting, roller, pickling or other methods should be used for surface cleaning according to the process requirements. The surface quality of the cleaned forgings should meet the requirements of the technical documents; the surface defects of the forgings are allowed to be cleaned, and the cleaning depth and aspect ratio are specified in the corresponding technical standards for forgings; when pickling is used for cleaning, the pickling solution should be regularly tested according to the corresponding technical documents. replace. Forgings are not allowed to be over-pickled.
Process inspection, each batch of forgings must be subject to the “first three inspections” system and can be officially put into production after passing the inspection. Strictly implement self-inspection, mutual inspection, and special inspection in production.
The process inspector should conduct a tour inspection on the production site, monitor the temperature control of the forging furnace and the forging operation, and regularly check the overall dimensions and surface quality of the forgings. After the forgings (or blanks) have passed the inspection, the inspector should sign the process card or record card before transferring it to the next process.
Final inspection of forgings and final inspection of die forgings shall be carried out in accordance with relevant regulations such as forging drawings and contracts. The final inspection of free forgings shall be carried out in accordance with the forging drawings and relevant provisions of the contract. It is acceptable to print inspection marks (or hanging labels) or other marks on the specified forging parts.
Qualification certificate, the qualification certificate should be filled out and issued by the inspection department according to the relevant technical standards or contract requirements.
Unqualified products, the forgings confirmed to be unqualified after inspection by the inspection department should be stored in isolation and handed over to the unqualified product processing agency of the quality assurance system for processing. In the production process, if quality problems are found, production should be stopped immediately and the analysis should be organized in a timely manner to find out the reasons and propose solutions or improvement measures.
Regularly conduct user (or next process) visits and timely research and process the comments and feedback information from users during the visit.
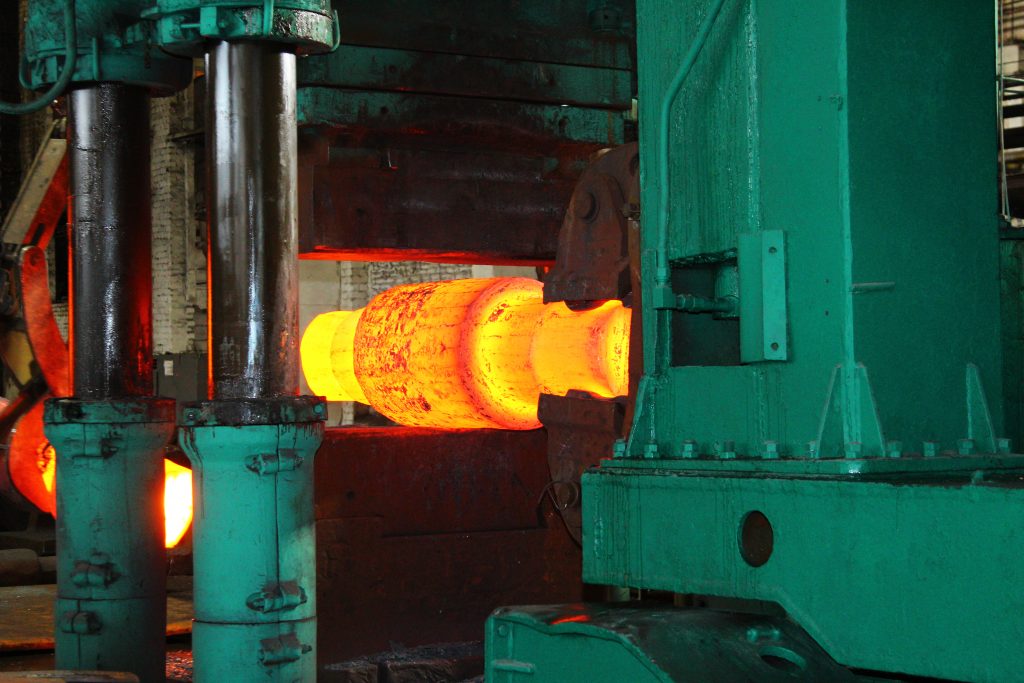